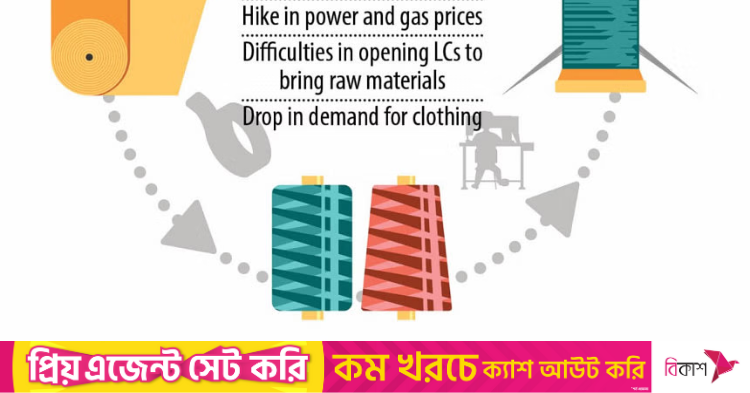
Listed apparel companies in Bangladesh struggled to capitalise on the massive devaluation of the local currency against the US dollar in fiscal year (FY) 2022-23 due to a hike in gas and electricity prices, and fuel and raw material costs.
The taka was devalued by 18 percent to Tk 108 per US dollar in FY23, data from Bangladesh Bank shows.
Listed spinning mills were among the worst performers as they had to absorb the double shock of higher fuel costs and higher import costs for raw materials.
Since most spinning mills do not export their products, they had no way to offset rising costs stemming from the devaluation of taka.
On the other hand, the export-based readymade garments (RMG) sector was able to offset higher costs of fuel and electricity as they raked in more money from exports due to the devaluation of the local currency.
This situation became more aggravated in the past quarter of FY24.
Mohammad Abdur Razzaque, research director at the Policy Research Institute, said the export-based RMG sector was only able to make profits because of the devaluation of the local currency.
“If the devaluation was not allowed, their situation would be even worse,” Razzaque said.
At the same time, an energy crisis has engulfed factories, with hikes in the price of fuel meaning they struggle to make higher profits, while inflationary pressures in the local and global arena have induced lower demand and hit sales.
Another important factor was that currency devaluation did not only occur in Bangladesh, but had been observed in many competitor countries.
“As a result, we were not the only ones who became more competitive,” Razzaque added.
Fazlul Hoque, former president of the Bangladesh Knitwear Manufacturers and Exporters Association, added that the RMG sector did not enjoy good business because raw material costs had risen by as much as 20 percent alongside other costs.
Moreover, inadequate supply of gas meant factories had to opt to buy diesel and other fuels.
“I think the massive price hike of gas had a big impact,” Hoque said.
The government hiked gas prices for power, industries, and commercial (hotel and restaurant) sectors by 179 percent in January 2022.
In the same year, electricity prices were raised twice, totalling to about a 10 percent increase, according to data from the Bangladesh Energy Regulatory Commission.
Moreover, high inflation rates in western countries led to a drop in demand for clothing, added Hoque, who is also managing director of Plummy Fashions Ltd.
“As a result, sales and profits of most apparel companies went down last year,” he added.
Export earnings, one of the major sources of foreign currency, amounted to $4.3 billion, up by about 10.4 percent year-on-year, according to data from the Export Promotion Bureau.
Of the 59 listed apparel makers, 10 saw their profit rise in FY23, four returned to profit, 18 saw lower earnings, nine remained in loss and seven did not publish their data.
Interestingly, 11 textile and RMG companies that had made profits the previous year recorded losses.
Mohammad Ali Khokon, president of the Bangladesh Textile Mills Association, told The Daily Star that most companies did not operate in full swing last fiscal year due to the gas crisis, shortage of raw materials and lower global demand.
Khokon added that banks could not open letters of credit as per the demand of producers and so, raw material imports were inadequate and production was subsequently interrupted.
“Due to the fallout from Russia’s invasion of Ukraine, demand for finished goods has dropped globally. So, it ultimately impacted all companies,” said Khokon, who is also chairman of Maksons Spinning Mills.
Among apparel makers, Maksons Spinning Mills incurred the highest loss of Tk 93 crore in FY23, followed by Ring Shine Textile’s loss of Tk 74 crore, Tallu Spinning Mills’ loss of Tk 25 crore and Prime Textile’s loss of Tk 22 crore.
Noor Mohammad, company secretary of Maksons Spinning Mills, added that yarn prices did not increase at a pace that would help them offset increased costs for raw materials and electricity.
Finance costs also increased so many companies struggled, he added.
New Asia Group, owner of Rahim Textile Mills and Malek Spinning Mills, echoed the same, saying its companies sunk into losses due to lower sales and higher raw material and power costs.
Rahim Textile Mill’s sales fell 17 percent year-on-year to Tk 146 crore in FY22-23.
It incurred a loss of Tk 12 crore in the last fiscal year after making a profit of over Tk 1 crore the previous year.
Malek Spinning Mills incurred a loss of Tk 22 crore in the last fiscal year after logging profits of Tk 86 crore the preceding year.
Md Sorafuzzaman, company secretary of Far East Knitting & Dyeing Industries, said his company’s profits rose mainly due to devaluation of the local currency against the US dollar.
However, a portion of that income was eaten into by higher fuel costs, he added.
The company’s profits soared 50 percent year-on-year to Tk 33 crore last fiscal year.
Paramount Textile Mills logged the highest profit among all listed apparel companies, registering Tk 122 crore, followed by Square Textile, which recorded profits of Tk 114 crore last fiscal year.