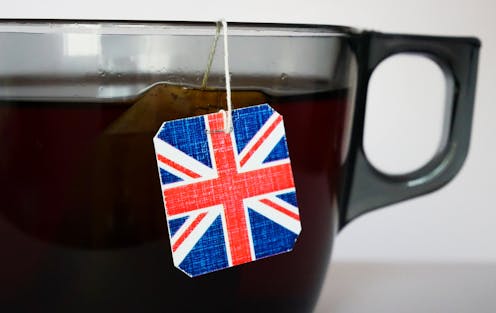
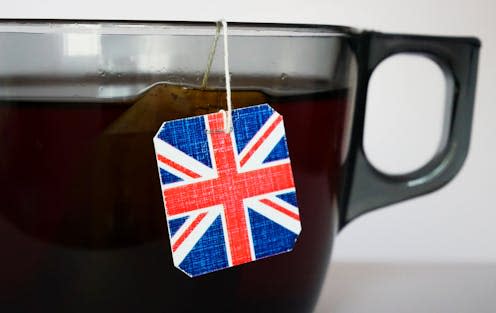
British people are known around the world for their love of tea. This is borne out by the statistics: a staggering 50 billion cups of tea are consumed on average in the UK every year.
Most of this tea is made using black tea leaves, most of which are not produced in the UK. Thus, shipping disruption caused by attacks on merchant vessels in the Red Sea, through which an estimated 12% of global trade passes each year, has sparked fears of a national tea shortage.
The attacks, which are being carried out by the Yemeni Houthi rebel militant group in support of Hamas, have forced shipping companies to redirect around the southern tip of Africa – a journey that can take up to three weeks longer.
Two of the UK’s biggest suppliers of tea, Tetley and Yorkshire Tea, have announced that they are monitoring their supply chains closely for any potential disruptions. And customers have reported reduced stocks of tea in supermarkets across the UK.
It is no surprise that tea is vulnerable to supply chain disruption. The tea supply chain is a complex global network, involving producers, processors, auctions and wholesalers, packers, distributors and retailers.
The UK imports primarily unprocessed tea from countries in south Asia and east Africa. This tea is then packaged and blended within the UK for both domestic and export markets. Only around 10% of the packaged tea sold in the UK is supplied by companies from overseas.
But tea is one of many items to be caught up in the supply chain crisis. The disruption is affecting supplies across various other sectors too, including electric cars and liquified natural gas – and it could prove costly.
The UK is particularly reliant on natural gas for the production of carbon dioxide, a gas that is essential for everything from NHS operations to keeping food fresh while it is transported.
Not so unpredictable
The disruption caused by the Red Sea attacks is considered by some to have been an entirely unpredictable occurrence of what is known as a “black swan” event. But this crisis is the latest in a long line of shocks to global supply networks that have occurred over the past decade.
Whether it was the 2011 tsunami off the coast of Japan, Brexit, COVID, US trade sanctions on China, or the war in Ukraine, the fact of the matter is that supply chains are now experiencing disruption more often than they used to.
There are two reasons for this. First, organisations have become increasingly reliant on distant countries for the manufacturing and supply of routine and critical components.
Sometimes this decision is made because of the natural advantage these countries hold. For example, China currently accounts for 93% of the global production of so-called rare earth elements, which are used in the components of many of the devices we use every day. But most of the time these decisions are driven by an organisation’s pursuit of lowering its cost of operation.
Second, a focus on just-in-time production, where businesses focus on producing precisely the amount they need and delivering it as close as possible to the time their customers need it, has reduced the buffer against supply chain shocks.
Building resilient supply networks
Organisations need to diversify their supply chains by developing alternate sources of supply. Many businesses already spread their source of materials over multiple suppliers across different regions to ensure quality, the continuity of supply, and to minimise costs.
For less complex components, such as packaging (cardboard, plastic bags and bubble wrap) or raw materials (metals and plastic), multiple sourcing is often practised through competitive tendering and reverse auctions; where the sellers bid for the prices at which they are willing to sell their goods and services.
However, for more complex products, the development of alternate sources of supply needs to be done strategically. One of the most important steps to improve supply chain resilience is to reduce reliance on global suppliers through processes called “onshoring”, “nearshoring” and “friendshoring”.
Onshoring is where components are sourced from suppliers located within domestic national borders. Nearshoring is a similar strategy where a company moves its supply to neighbouring countries. And friendshoring is where organisations transfer their production away from geopolitical rivals to friendlier countries.
The US, for example, has traditionally relied on Taiwan and South Korea for its supply of semiconductors (computer chips). But geopolitical tensions with China, coupled with a global shortage of semiconductors, have forced the US to look for suppliers in countries closer to home, while also exploring the potential of moving chip manufacturing to the US.
Geographical and climate factors restrict the onshoring of tea cultivation to the UK. But these supply strategies could help businesses manage the risk of supply chain disruption to other, potentially more critical, commodities.
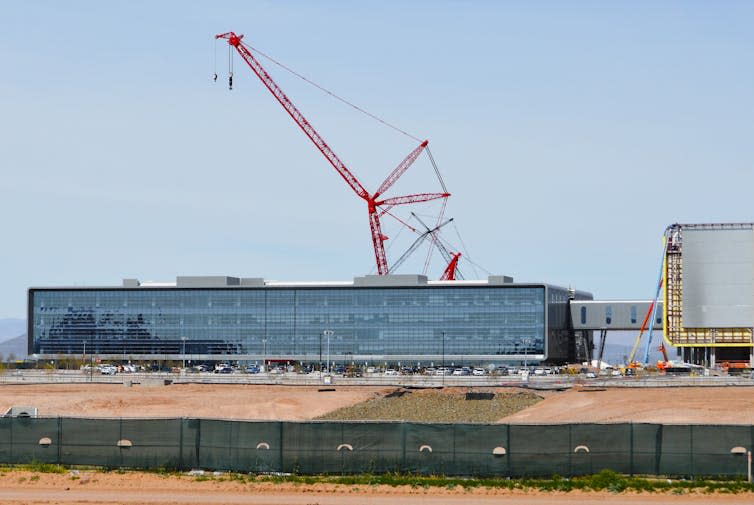
Making supply chains more agile
The frequency with which global supply chains are now becoming disrupted means that organisations must rethink their supply chain strategies, evolving from being efficient and lean to flexible and agile.
An agile supply chain strategy will require businesses to maintain adequate inventory levels to guard against a situation where stock runs out. These inventory levels must be informed by real-time – or as close to real-time as possible – data on customer demand.
The disruption to the UK’s tea supply highlights the vulnerability of supplies of everyday essentials to unexpected events. But businesses can make sure they are better prepared for the occurrence of an unexpected event by enhancing the resilience of their supply chain through diversification and agility.
This article is republished from The Conversation under a Creative Commons license. Read the original article.

Jas Kalra does not work for, consult, own shares in or receive funding from any company or organisation that would benefit from this article, and has disclosed no relevant affiliations beyond their academic appointment.