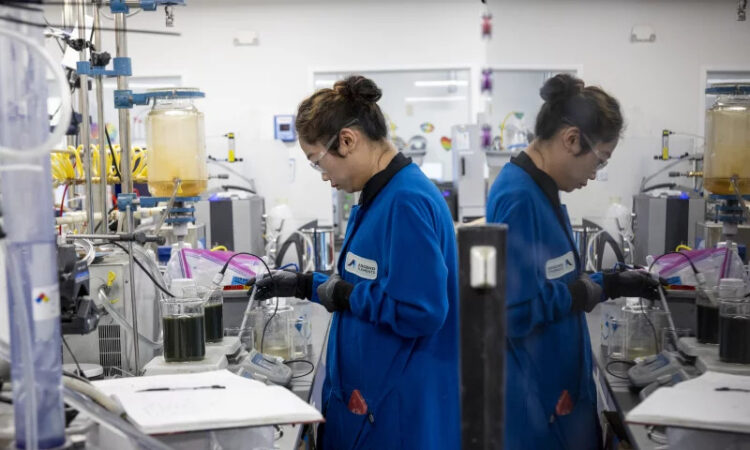
Plastic bags of dark powder sit on a metal shelf. The powder contains minerals that came from lithium-ion batteries and are destined to be made into batteries again. That, in itself, is not revolutionary.
But where this shelf is located — in an unassuming industrial park an hour west of Boston — symbolizes how the battery-recycling industry is on the cusp of change.
Today, key steps in the battery-recycling process mostly happen overseas, particularly in Asia. Companies there have spent years building up a battery supply chain in which recycling and building batteries are closely connected.
But more and more batteries spend their lives powering electric vehicles in the United States. Shipping minerals halfway around the world costs money, creates carbon emissions, adds supply chain risks and, from the U.S. perspective, pushes some jobs and profits overseas.
That’s why the U.S. government is pouring money into an effort to bring the whole battery-recycling ecosystem to the United States. Meanwhile, automakers and battery companies, as they build new battery and EV plants across North America, want recycling close by; they’ll have a lot of batteries to scrap in the years ahead as electric vehicle sales rise.
These minerals in their 25-pound plastic bags, recycled by a company called Ascend Elements, epitomize the new geography of battery recycling. They were ground up in Georgia, processed in Massachusetts and headed to Michigan for manufacturing — every step happening in the United States.
Keeping battery minerals closer to home
Lithium-ion batteries are hazardous waste if they’re discarded, but they’re a valuable resource if they’re recycled.
Because they’re hazardous, some states legally require battery recycling. And because they’re valuable, EV batteries are often recycled even where it’s not mandated: Vehicle dismantlers can sell the batteries for money.
But how does it work? Step 1 is safely collecting batteries, discharging them and then disassembling and shredding them. The result is a black powder that’s called “black mass” in the battery-recycling industry. This happens at locations scattered across the U.S., including at an Ascend Elements facility in Georgia.
Then that powder of jumbled-up minerals is frequently shipped overseas to get turned back into something useful. In Westborough, Mass., Ascend Elements is doing those steps closer to home. The powder gets combined with sulfuric acid, where some minerals dissolve and others don’t, making it easier to sort them apart.
Ascend takes out (and in some cases, sells off separately) everything except the nickel, cobalt and other costly minerals that go into a battery’s cathode. The levels of each mineral get fine-tuned, and the mixture is dried back into a powder again.
Last month, the company began shipping the powder coming off the line — precursor cathode active material (pCAM), to use its technical term — to a buyer that will put the material into batteries for heavy-duty vehicles. Ascend believes this is likely the first time that pCAM made wholly in the U.S. from recycled materials is being used in commercial manufacturing.
Newer, cleaner processes for recycling batteries
In some cases, recycling processes, not just locations, are also changing. An older method relied on burning battery materials, which wasted many of the minerals and created pollution.
A newer method involves dissolving the minerals in acid instead, recovering more minerals with less waste (or potentially no waste, if companies reuse water and find uses for all their chemical byproducts). “Recyclers all across the world are adopting this technology,” says battery expert Beatrice Browning.
Meanwhile, Ascend is skipping several steps by not isolating all the minerals separately, like most acid-based processes do. “That’s extracting 98% of the material because you’re worried about the 2% of impurities,” co-founder and Chief Technology Officer Eric Gratz explains. “So we flip the problem around, and we’re extracting the 2% of impurities and keeping the nickel, manganese and cobalt together.”
Imagine you have a large Lego creation and you want to make a different Lego creation. Melting the whole thing down would be a brute-force waste of energy. Taking it apart and sorting all the bricks is more finicky but much more effective — like extracting out each mineral one by one. What Ascend is doing is more like breaking it down but not sorting all the bricks, just keeping them together in a big pile.
Meanwhile, some companies are working on a form of recycling called “direct recycling” that would take the battery apart without shredding it at all. It’s like keeping big chunks of Lego bricks together and reusing them as a single unit. And still other companies are exploring new ways to use electricity or other technologies to refine how metals are, well, refined.
A dual purpose: cutting emissions, boosting profits
Ascend’s production line is built right behind the company’s research and development lab, where Matthew Valdiviezo is watching a vivid teal liquid spin in a beaker as he explains that chemistry is all about rules. And his work is all about manipulating those rules — “to make us money in the long run,” he says, “and help the planet, of course.”
For many environmentally conscious drivers, battery disposal is a major concern. And it’s true that if batteries wind up in landfills, they would be a serious problem. But environmental advocates see a huge opportunity in recycling.
“Battery recycling can play, in the long run, a really big role in making electric vehicles more sustainable,” says Dale Hall of the International Council on Clean Transportation. “Decades from now, we’ll need very little new virgin raw materials to build new EVs. And that’s very different from what you have now with combustion engine vehicles, where you’re going to always have to be producing new virgin oil and feeding tons and tons of that into the vehicles over their lifetime.”
Meanwhile, Valdiviezo’s other motivation — the bottom line? That’s real too, and lots of other companies are chasing it.
Redwood Materials, started by a Tesla co-founder, is building multibillion-dollar plants in Nevada and South Carolina. “There is an incredible opportunity to create this closed-loop supply chain here domestically for the first time,” the company’s vice president of government relations and communications, Alexis Georgeson, told NPR in an interview earlier this year.
And, she noted, battery recycling is profitable today.
Cirba Solutions, another big player, is working on plants in Ohio and South Carolina. “We’re building as fast as we humanly possibly can build,” says CEO David Klanecky. “And I think we’re going way too slow, to be honest with you.”
‘It’s not fast enough‘
The pressure for speed might seem counterintuitive. EV batteries can last more than a dozen years (maybe much longer — the first mass-market EVs aren’t old enough to have much data beyond that). Some outlive their vehicles and could have a second life, like storing backup power for a building. And there aren’t that many EVs on the roads — yet.
But EVs from the first generation are starting to reach the end of their lives. Recalled batteries or those damaged in vehicular accidents also need to be recycled, as does scrap material coming from the production lines of plants manufacturing new batteries. Meanwhile, the nascent battery-manufacturing industry in the U.S. is hungry for materials, especially ones that meet made-in-America requirements for federal incentives.
That’s pushing companies to move fast. “Two years ago, there was nothing in here,” says Ascend senior process engineer Zain Nasir at the plant in Westborough. “The amount of hours everybody’s put in trying to get this place to where it is is just incredible.”
In the lab where she was testing products to confirm their quality, Rebecca Neslusan laughed when I asked her about the timeline. “The pressure is on,” she said. “As fast as we can do it, it’s not fast enough.”
In fact, the milestone that Ascend hit in June — that first commercial shipment out of this manufacturing line — is itself proof of the sense of urgency. For a chemical plant, the production line here in Massachusetts is tiny. It was originally meant to be a pilot, a proof of concept. But the demand is too high.
“We’re shipping here because the customer wants and needs the material as soon as possible, you know, basically faster than we can build our facilities,” says Gratz, the company’s co-founder and CTO.
His billion-dollar plant in Kentucky is due to open early next year.